International Journal of Aerospace and Lightweight Structures (IJALS)
Volume 1 Number 1 (2011)doi: 10.3850/S2010428611000092
High Velocity Perforation Simulations of Lightweight Target Plates Using a Modified Johnson-Cook Model
ABSTRACT
Because of their superior ballistic and mechanical properties, lightweight materials like titanium alloy Ti-6Al-4V and aluminum alloy AA5083-H116 have been frequently used for aerospace and military applications. Tests of ballistic limit velocity are limited by expensive nature of the experimental setup, and indeed, that can be resolved by adopting numerical simulations. Numerical study involving the finite element method (FEM) suffers from severe element distortion problem when used for high velocity impact analysis. Therefore, the coupled smooth particle hydrodynamics — finite element method (SFM) has been adopted to study the perforation of Ti-6Al-4V and AA5083-H116 target plates with thicknesses of 26.72 mm and 25 mm, respectively. In the SFM, smooth particle hydrodynamics (SPH) method is incorporated in the severely distorted regions and the FEM otherwise. Effects of strain rate and adiabatic heating are significant for high velocity impact problems, and hence, a constitutive model incorporating effects of high strain rate and adiabatic temperature is proposed. The constitutive model is verified and finally adopted for perforation studies. Close correlation between the numerical and experimental ballistic limit velocities are accomplished. The study shows that the proposed method is able to emulate the failure mechanisms of the target plates without any numerical problem.
Keywords: Element distortion, Finite Element Method (FEM), High velocity impact, Perforation, Smooth Particle Hydrodynamics (SPH), Titanium alloy.
FULL TEXT(PDF)

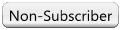