International Journal of Aerospace and Lightweight Structures (IJALS)
Volume 2 Number 3 (2012)doi: 10.3850/S2010428612000402
Experimental Study on Hot Bending of Ultra High Strength Steel 22Mnb5 and its Lightweight Application
Dalian University of Technology, Dalian 116024, P. R. China.
Dalian University of Technology, Dalian 116024, P. R. China.
ABSTRACT
Hot stamping temperature has significant effect on the mechanical property especially bending formability of 22MnB5. Focus on the optimal forming temperature zone of process, special V-shaped hot bending experiment was designed and different thicknesses sheets after heating to 950°C, 5 min were bended at different quenching conditions. The hardness and microstructure features after hot bending and spring-back behavior for sheet through temperature changes were investigated. The result showed that forming temperature between 600 - 700°C would contribute 22MnB5 sheet bending formability which spring-back angles are the smallest and the martensite texture formed was much finer. The real hot forming anti-collision beams test validated the optimal forming temperature between 600 - 700°C contribute the real hot forming process simultaneously. Furthermore, 22MnB5 hot forming parts through body mass optimal process are applied to analyze the potential mass reduction valuation of the BIW under bending condition, by using VCD-ICAE, a self-developed and entirely parameterized BIW concept design system. The conclusion showed the application of hot forming component replace traditional part not only raise the stiffness and modal index, but also could reinforce strength of body of BIW and make vehicle more lightweight and safer at the same time.
Keywords: Hot forming, 22MnB5, Hot bending formability, Lightweight, VCD-ICAE.
FULL TEXT(PDF)

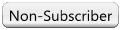