Keynote Speakers
doi:10.3850/4M2009RP001_9005
Carbon Nanotube Composites for the Micro-World: Design for Functionality and Manufacturability
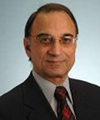
Dr. Shiv G. Kapoor
Department of Mechanical Science and Engineering,
University of Illinois at Urbana-Champaign, USA
Biography
Dr. Shiv G. Kapoor is Grayce Wicall Gauthier Chair Professor in the Department of Mechanical Science and Engineering at the University of Illinois, Urbana-Champaign. He has been a significant contributor to the field of manufacturing engineering research and education and a pioneer in the field of mathematical modelling and simulation of machining processes both at micro and macro-scale.
He has published more than 200 technical articles in technical Journals including ASME Journal of Manufacturing Science and Engineering, Transactions of the North American Manufacturing Research Institution, International Journal of Machine Tool and Manufacture , International Journal of Wear, Journal of Corrosion Science, etc. The funding for his research program has come from both government agencies including the National Science Foundation, the National Institute of Standards and Technology, the Department of Energy, the Department of Defense, and companies, including Motorola, John Deere, Mori Seiki, General Electric Corporate Research and Development, Caterpillar, Inc., General Motors Research Laboratory, Ford Motor Company Scientific Research Laboratory, and Kennametal Inc.
A Fellow of both the American Society of Mechanical Engineers (ASME) and the Society of Manufacturing Engineers (SME), Prof. Kapoor has received the ASME’s Blackall Machine Tool and Gage Award for an outstanding research paper in 1992, 1997 and 2008. He was given the ASME William T. Ennor Manufacturing Technology Award in 2003 and one of the SME’s most coveted Education Award in 2005. He currently serves as an editor-in-chief for the Journal of Manufacturing Processes.
Abstract
Carbon nanotubes (CNTs) are an ideal reinforcement phase for composite applications at the micro-scale. These include specific use in the areas of biomedicine, electromechanical actuators and electrically-conductive polymers. The objective of this paper is to highlight the importance of developing a knowledge base that will enable the design of CNT composites to meet both the micro-scale engineering and manufacturing/machining requirements. To this end, significant results from recent experimental and modeling research on the machining of CNT composites are presented. CNT loading, alignment, dispersion and the interfacial bonding between the CNTs and the matrix have a strong influence on the functionality and machinability of CNT composites. Micro/meso-scale machining studies reveal that an increase in CNT loading improves the machinability of the composite. Visco-elastic/plastic deformation of the polymer-phase plays a significant role while machining the composite with 1.75% CNT loading, whereas for CNT loadings ≥ 5%, the CNT distribution and interface failure effects were found to be important. Microstructure-based CNT composite machining model is presented and model predictions are discussed. This model serves as a design tool to identify critical microstructural parameter combinations of CNT loading, alignment and dispersion that result in favorable machining results. These results were then used to show how the morphology of the machined surface could be harnessed to produce the next generation of micro-fluidic devices with self-mixing capabilities.